How to know how many pole pairs my motor has?
Problem
It is quite a common problem to have a motor without its datasheet (or with it but incomplete information) and wonder how you can get to know some of the parameters. In this article, we are going to show you how you can determine the number of pole pairs of your motor. Take for example, that you have a motor whose parameters are the following:
However, let's act like we don't know the number of pole pairs. In that case, what process can we follow in order to determine it?
Steps
- First of all, take a look at the feedback device that you are using, and make sure that you have it properly configured in MotionLab. Once you have ensured this, try to calculate how many position "counts" are needed in order to do a mechanical revolution of the motor. This can be done if you have information about the total resolution of the feedback device or if you can move the motor manually a whole revolution and reading how much the "Actual position" changes in the feedback window. If you have a gearbox in your system, take into account the gear ratio between the motor and the output so that you get the right amount of counts (you will be counting one revolution on the output most likely). In this example we are going to use a single-ended 1000 ppr encoder like the one that is shown in the following picture:
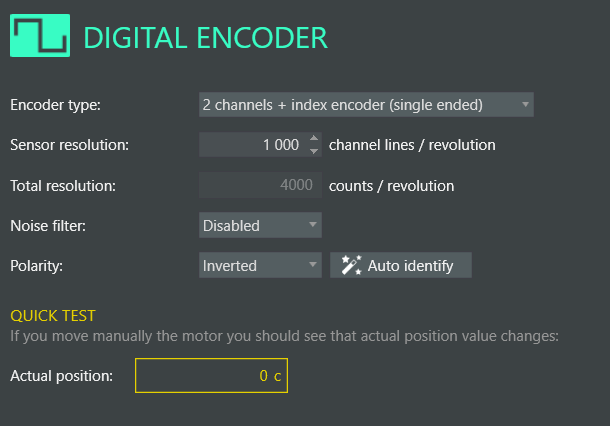
If you don't know the resolution of the motor, don't worry about it, you can still determine the number of pole pairs but you will be a little bit more accurate in the next step.
- The next step will be to use the Open-loop with "Internally generate commutation angle" mode in order to move the output shaft (the motor or the one after the gearbox) one full revolution. In order to do that, proceed to apply a target voltage in the 0-20% range and a target frequency in the 250-1000 mHz range so that the motor can start to move slowly but steadily (depending on the motor you might need to increase it a little bit more). After you enable the motor, you will get it moving at a slow and controlled pace.
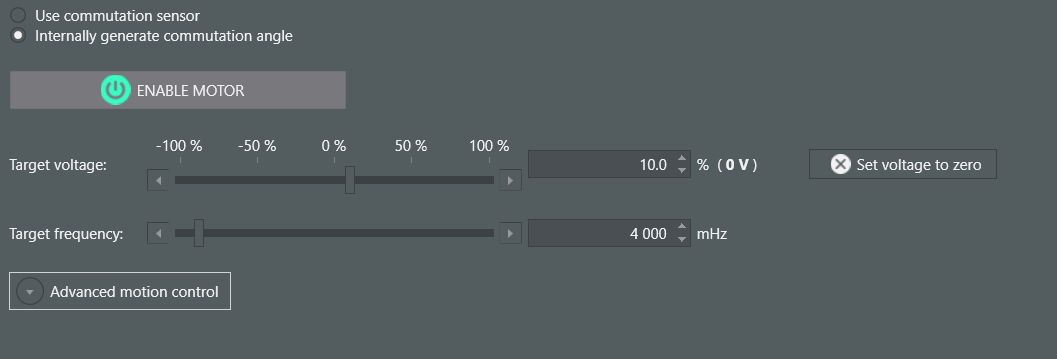
- Once you get the motor moving, you need to open the Scope and plot the following registers while the motor is moving: Position actual value and Current phase A. Then what you need to do is count one full revolution and then see how many cycles the current of phase A has done in that time. This number of cycles is directly the number of pole pairs that the motor has. In the case of our example, we needed to see how many cycles the current did during 4000 encoder counts and that can be seen in the following picture.
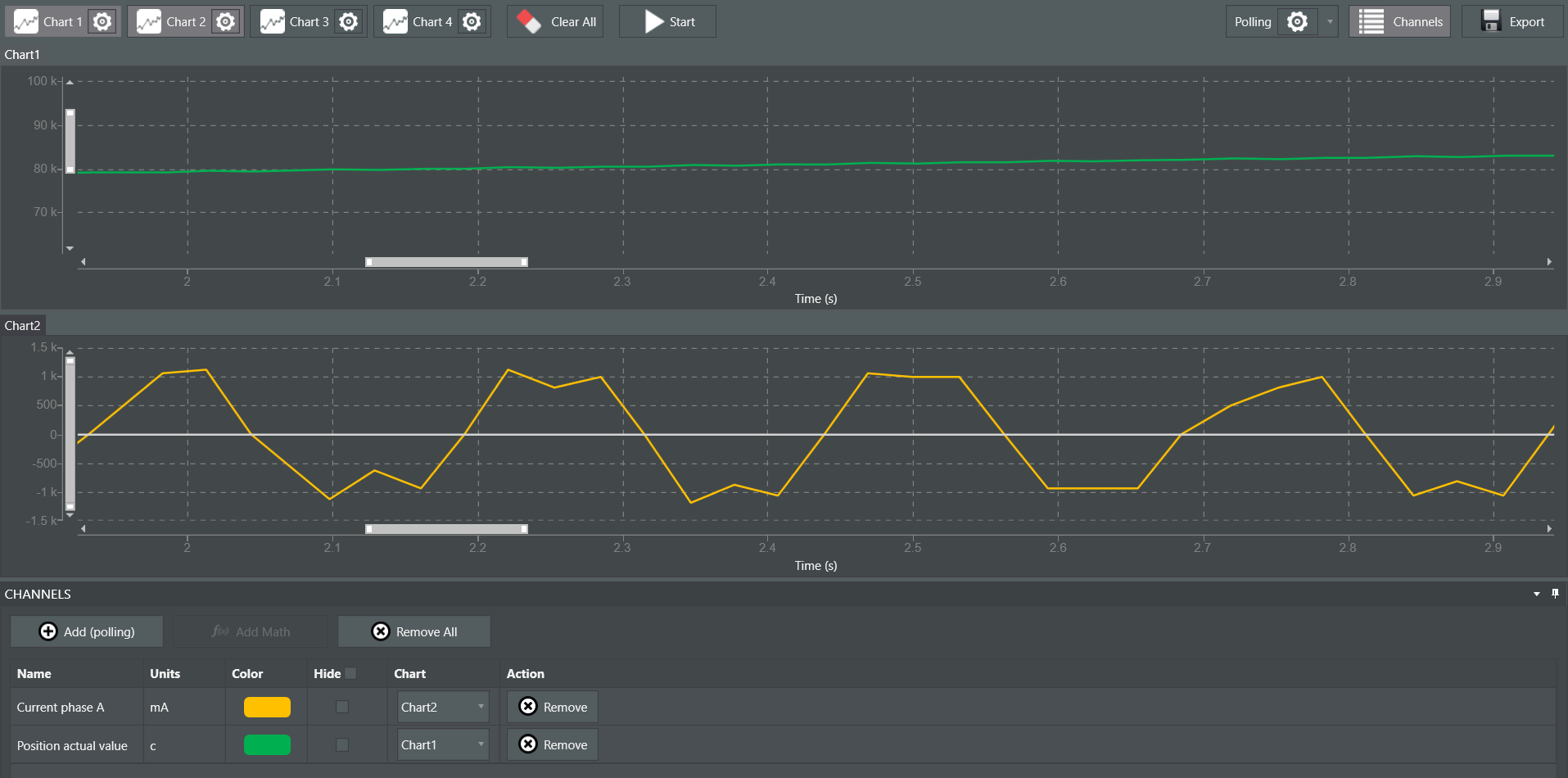
- As it can be seen, the number of cycles is 4 and that matches the number that we had at the start of the article. In case we didn't have the resolution of the feedback device clear, what we would need to do is plot the current of the phase only and make sure to start and stop the Scope once the revolution has been performed (which we will need to control with our own eyes).
- In case you had a gearbox in the system as well, you will need to divide the number of cycles that you counted for one revolution at the output shaft by the gear ratio in order to get the proper number of pole pairs. For example, if I had had a gearbox with a 10:1 ratio, I would have read 40000 counts at the output and 40 cycles in total so I would need to divide that number by 10 in order to get the 4 pole pairs that the motor actually has.
Related Articles
How to configure a rotatory brushless motor with resolver feedback
Problem I have a rotatory brushless motor with resolver as feedback but I don't know how to properly configure it and tune it. What is the right process that I need to follow? Clarifications and checkings This step by step process assumes that your ...
How to know if the motor phases or the power stage of the drive are damaged
Problem I have a motor connected to the drive and I want to check that it is fully capable of moving. I want to check that both the motor phases and the power stage of the drive are not damaged. What can I do to check this? Steps The first step is to ...
How to configure a brushed DC motor
Problem I have a rotatory brushed DC motor with a certain feedback device but I don't know how to properly configure it and tune it. What is the right process that I need to follow? Clarifications and checkings This article describes (step by step) ...
Why does my brushless motor not reach rated speed?
Problem I have already configured my motor completely with the Configuration Wizard (or manually) but when I try to move the motor, I can see that it clearly does not reach its rated speed. Why does that happen and what can I do about it? Before ...
What to do when your motor does not move
Problem I am trying to move my motor with an Ingenia servo drive with MotionLab but I can't manage either to make it move or move it in the controlled way that I want. What can I do to solve this? Solution This is quite a complex problem that can be ...